Critical Gas Surface Interaction Problems for Atmospheric Entry
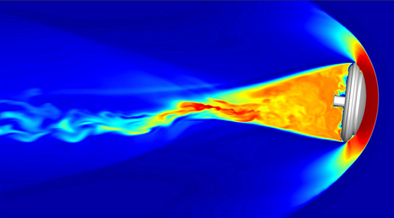
This work focuses on three critical issues in the area of gas-surface interactions that need to be resolved to improve entry descent and landing systems for future planetary exploration missions of interest to NASA: 1) quantifying catalytic recombination rates for Mars atmosphere plasmas; 2) quantifying nitrogen recombination rates on high-temperature carbon-based heat-shield material surfaces; and 3) developing an approach for measuring energy accommodation on materials resulting from surface-catalyzed recombination reactions. A combined numerical and experimental investigation will be undertaken to resolve each of these critical issues. Experiments will be performed on relevant materials in the 30 kW Inductively Coupled Plasma (ICP) Torch Facility and spatially resolved laser spectroscopic measurements will be used to quantify recombining and recombined species fluxes at the material surface for appropriate plasma conditions. A numerical model coupled with a high-temperature gas property library (MUTATION++) will be used to model the ICP torch facility tests and provide additional information to complement experimental measurements and to inform the design of additional experiments. Molecular dynamics simulations of key reactions will be used to aid in the evaluation of recombined species leaving the surface. The overall effort will include both research and educational activities. This proposed investigation will strengthen ongoing collaborations with two NASA centers that have strong interest in this topic (Ames and Langley Research Centers).
Evaluation of Pyrolysis Gases and Plasma Reactions
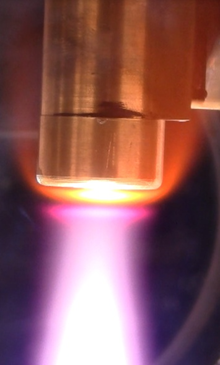
The pyrolysis mechanics of Phenolic Impregnated Carbon Ablators (PICA) makes it a valued material for use in thermal protection systems for spacecraft atmospheric re-entry. This study of the interaction of pyrolysis gases and char with plasma gases in the boundary layer over not only PICA, but its substrate, FiberForm, as well. Exposure of these material samples separately to argon, nitrogen, oxygen, air plasmas, and combinations of said test gases provides insight into the evolution of the pyrolysis gases as they react with the dierent plasmas. Measurements done to date include time-resolved absolute emission spectroscopy, location-based temperature response, and more recently, spatially resolved and high-resolution emission spectroscopy, all of which provide measure of the characteristics of the pyrolysis chemistry and material response. Tests with relatively inert argon plasmas established a baseline for the pyrolysis gases that leave the material. CN Violet bands, NH, OH and Hydrogen Alpha (H-a) lines were seen with relative repeatability in temporal, spectral, and intensity values. Tests with incremental addition of reactive plasmas (diluted nitrogen and oxygen) provided a preliminary image of how the gases interacted with atmospheric flows. Evidence of a temporal relationship between NH and H relating to nitrogen addition is seen, while oxygen addition sharply reduced the signal of previously seen pyrolysis gases. Temperature analysis highlighted the reaction of the material to oxygen addition and displayed the in depth material response to argon and air/argon plasmas. The development of spatial emission analysis has been started with the hope of better resolving the previously seen.
Electron Transpiration Cooling of Hot Aerospace Surfaces
One major limiting factor in the maturation of advanced hypersonic technologies and flight systems is the state of advanced thermal mitigation strategies. The need for effective thermal management techniques on aerospace vehicles is a factor limiting overall mission performance when critical vehicle components experience out-of-tolerance heat fluxes. Hot aerodynamic surfaces inherent with hypersonic platforms require significant cooling to retain shape-stable characteristics. Ablative technologies can absorb these high heat fluxes on a one-time basis, but their ablative nature precludes their use as aerodynamic surfaces. Current refractory Ultra-High Temperature Ceramic (UHTC) materials are able to retain their shape at high heating levels, but only in limited flight trajectories. Moreover, they are quite dense and brittle. However, despite their limitations, many research entities are actively developing UHTCs for hypersonic systems. What is needed is a novel thermal mitigation strategy that will give a substantial performance edge and wider trajectory range to emerging hypersonic platforms.
One novel thermal-management approach involves a thermo-electric material—a ceramic electride—that can generate a free electron flux when heated to high temperatures, leading to transpiration cooling of the material. This phenomenon, known as electron transpiration cooling (ETC), occurs when the thermal energy of the electrons (the temperature of the material) is greater than the binding potential of the material surface. The goal of ETC is to provide a heat rejection method for hot surfaces—whatever their application—that can reject more heat, with lower volume and mass requirements, than other techniques, while maintaining a stable surface shape. However, for ETC to be realized practically, a material of sufficiently low work function and oxidation resistance must be developed and tested.
Thermal management is also a factor limiting the performance of other critical technologies, such as aircraft turbine engines, and dual-use and commercial technologies such as power conversion and nuclear isotope production. Taken together, the challenges in these spaces represent economic and defense cost improvement potential of billions of dollars.
Gas Surface Interaction Studies on Flexible Thermal Protection System Materials

Heritage thermal protection system (TPS) strategies for planetary atmospheric entry make use of rigid aeroshells that are constrained by launch vehicle shrouds and cannot provide sufficient surface area to slow down payloads of significant mass such as a human-¬scale lander. Today, a 4.5 m diameter heat shield lands a vehicle that weighs approximately 900 kg and can only access 30 to 40 percent of Mars and restricted to landing below “sea level” to take advantage of higher atmospheric density. Future human space exploration missions require the precise landing of larger payload masses – 40,000 kg, 8x8x20 m for Mars entry. However, as payload masses increase, so too do the heat loads to the entry vehicle. This requires a need for TPS with increased heat shield geometries coupled with state of the art materials. Increasing the diameter of a heat shield augments the effective ballistic coefficient (vehicle mass normalized to heat shield area) thereby mitigating the heat load experienced during the hypersonic flight phase of entry. However, maximum heat shield size is limited by existing launch vehicle shroud diameters that carry these payloads. Reliance on heritage strategies to mitigate thermal heating experienced by planetary entry vehicles can ensure recurring success of lower mass payload entry but will limit advancements in science and technology necessary for future high mass missions.
This assessment has led to advanced research initiatives such as NASA’s Game Changer technology programs. One game changing concept to help circumvent this TPS geometry restriction is by making use of deployable systems. A deployable TPS is a system that is compact at launch meeting the geometric constraints of the launch vehicle shroud. Once the vehicle is near the entry interface the TPS deploys to a larger diameter thereby increasing the effective vehicle ballistic coefficient. Two deployable TPS strategies are at the heart of NASA’s entry of high payload mass interests: mechanical and inflatable. Both systems are folded for launch and deployed before planetary entry, providing the essentially rigid aerodynamic surface and heating protection needed for hypersonic deceleration, at a scale up to 25-30 m.